Aerospace Case Study
See how Export Corporate resolved a complicated problem for one of our aerospace clients.
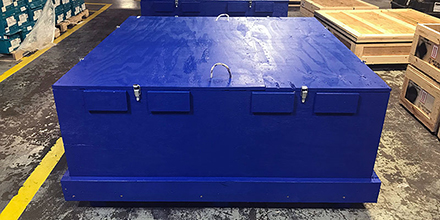
See how Export Corporate resolved a complicated problem for one of our aerospace clients.
An aerospace engine supplier manufactures and assembles a jet engine part valued around $80,000. They were using a complicated wood box that was difficult to handle, required a lot of floor space, and was costly upfront and in shipping weight. Above all, it was made of low grade lumber that left shards of wood, dust and a mess in the end customers white facility where final jet engines are assembled.
We went onsite to review the problems, take dimensions of the part, and gather all information necessary to design a custom wood box. In under 2 days, our packaging engineer designed a custom wood box using higher quality and significantly less lumber than the previous solution.
Not only does our wood box cost 40% less than the previous solution, both our customer and their end customer have significantly reduced the amount of handling and labor involved with the packaging. This also resulted in lower shipping costs, use of less floor space at both facilities and above all it is now a returnable container due to the overall quality of the wood box.
Send us details about a packaging project you need, and a member of our expert team will be in touch.